
Revealing the fractured ice of Antarctica’s “Doomsday Glacier”
Dr Jamin Greenbaum and the team are working at the front line of climate change on the coldest continent on ...
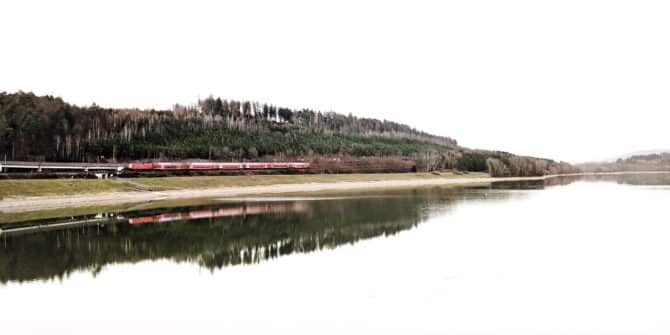
Prof. Quick und Kollegen establish BIM workflow for new German high-speed railway line
A new high-speed traffic line in Germany, will eliminate bottlenecks and shorten journey times to serve an increase in passengers ...
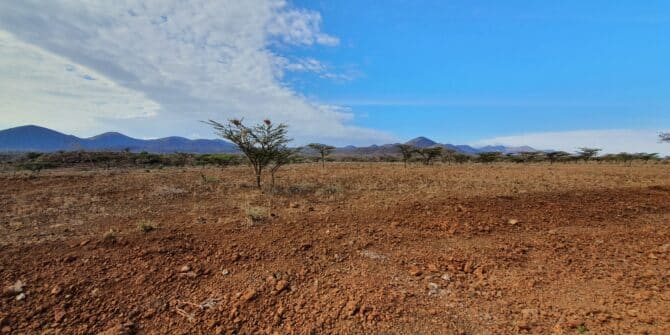
Kenya Nationwide Airborne Geophysical Survey brings crucial insights into mineral, groundwater and geothermal resources
The Kenya Nationwide Airborne Geophysical Survey (KNAGS) captured over three-million-line kilometres of magnetic, radiometric and in-line high density dGPS data ...
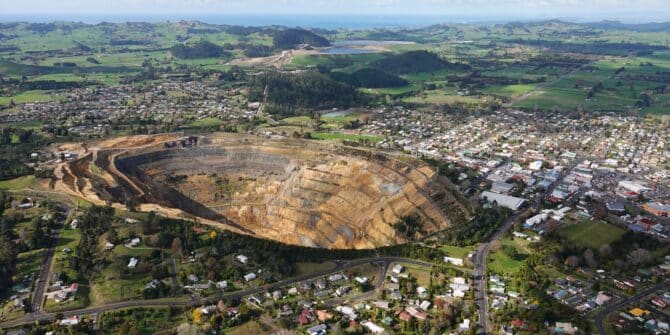
OceanaGold pilots innovative digital response for managing the Waihi Tailings Storage Facility
In an industry striving for best practice in Tailings Storage Facility management, OceanaGold’s digital response to their Waihi operations offers ...
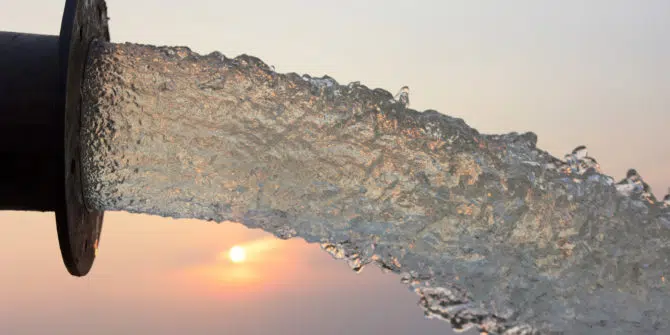
Rehearsing the hunt for water in the volcanic tuffs of Somotillo
To help the Living Water teams become shrewder and sharper well-hunters with Res2DInv, the organisation arranged a training session in ...
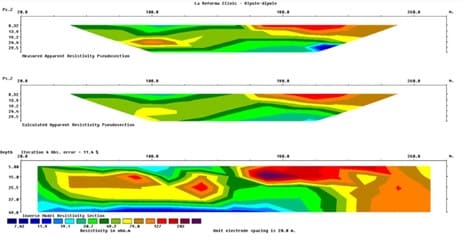
When in doubt, follow the science, find the water
Seequent’s geophysical inversion software AGS Res2DInv has been the key to unlocking bigger, better water supplies for parched communities across ...
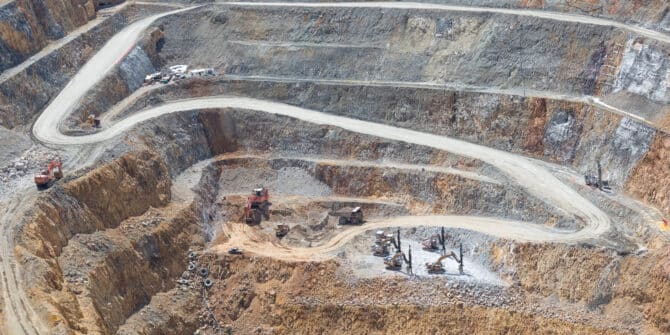
How digital transformation enables Hanson Australia to further unlock the value of their geological data.
This article originally appeared in Quarry Magazine. Hanson Australia is a leader in building and construction materials with a vision ...
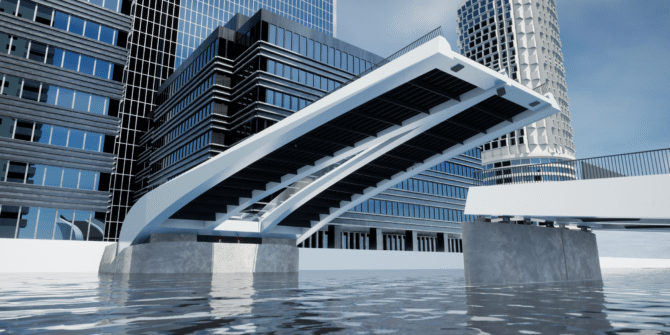
Arcadis leverages innovative digital solutions to design London’s South Dock Bridge
The bustling financial district of Canary Wharf in the United Kingdom will soon feature a brand-new pedestrian crossing set to ...