Mining is high risk at every stage: you must find the minerals, safely and efficiently extract them, and ensure minimal environmental impact.
Mining and exploration companies have long used airborne and ground-based geophysics surveys to reduce costs and risks.
Resistivity modelling can identify groundwater for use and protection, help locate mineral deposits, identify targets for drilling programs, as well as inform the placement of tailings dams.
“From the beginning our software was designed to support large data sets from airborne surveys,” says Toke Søltoft, director and geophysicist at Aarhus GeoSoftware (AGS, a part of Seequent).
“The software helps miners distinguish where there are mineral bodies, different kinds of bedrock, groundwater, or clay that can cause landslides.”
AGS software can use data from all geophysical instruments for electromagnetic and resistivity surveys, and as well as provides tools for groundwater mapping.
“We also support ground-based surveys in mineral exploration to create resistivity models. If there’s local geological knowledge of the mineral bodies, drillholes for example, you are able to use that to constrain resistivity models.”
Combining different types of geophysical data into resistivity models adds clarity to the subsurface.
Here are five ways mines are using AGS to reduce risks, costs, and make better decisions:
1. Discovering minerals
Lithologies, bedrock, and different metals all have different resistivities depending on their unique chargeability. Clay, for instance, has low resistivity.
Survey data can be used to scan a large area and discover regions that have differing resistivity, and use that information to identify mineralised zones.
“Mines are using our tools to locate kimberlite bodies, gold, carbon, nickel deposits, and others. Often, they combine AGS resistivity models with magnetic, gravity data, or even seismic data.”
Resistivity models can also help constrain drilling projects by helping define areas of interest. Why drill where there are no minerals? Mines and exploration companies can improve drilling programs using their resistivity models.
“We have a GIS interface you can use to put your resistivity data onto maps, so you can have a better visual idea of where the mineral bodies are located.”
Groundwater, too, can have different resistivities and chemical content, and can be used to inform what types of minerals might have formed nearby. This provides valuable information to geologists searching for clues during exploration.
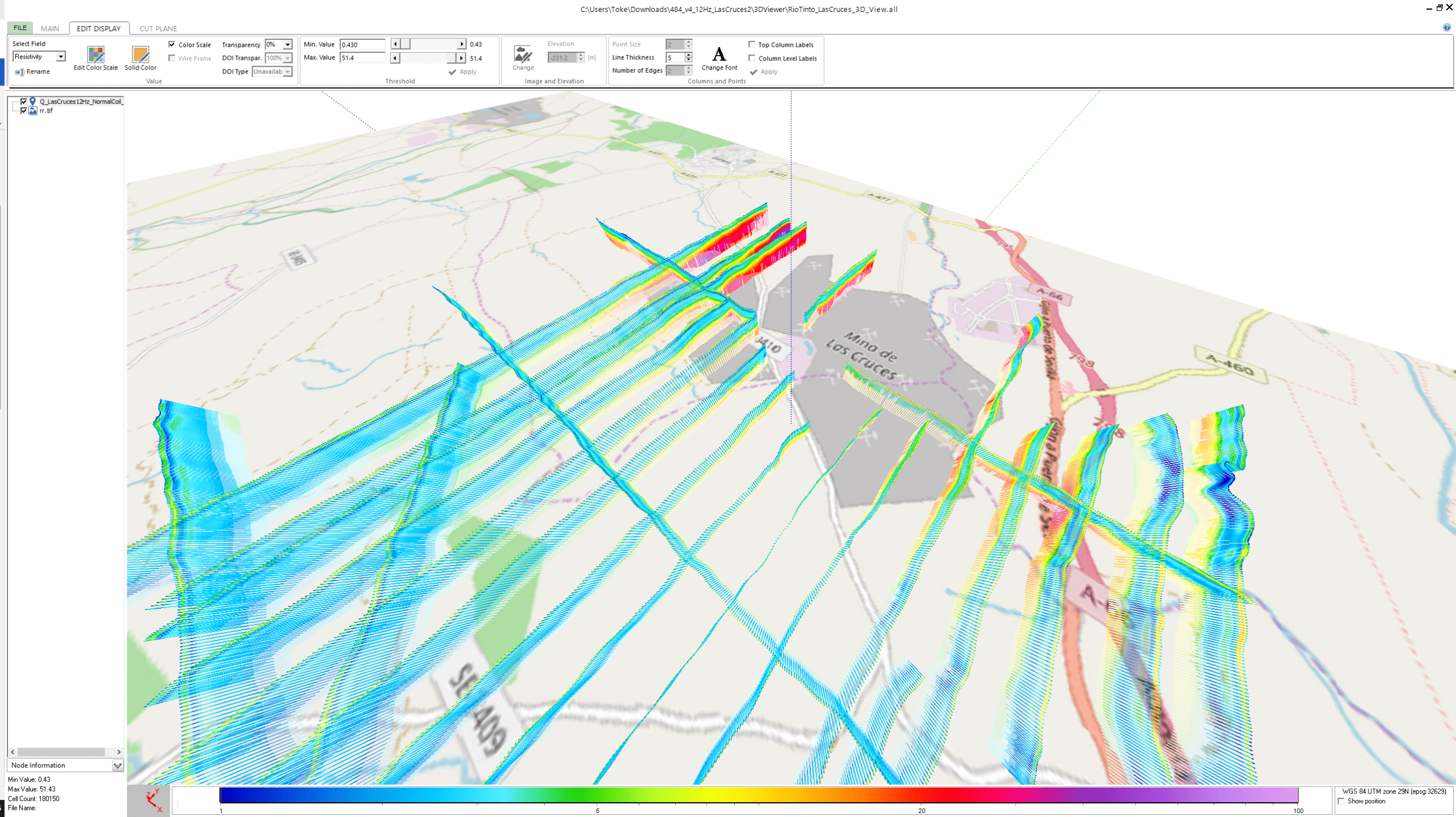
Resistivity models in 3D viewer for a mining survey.
2. Better data, better models
Geophysics data can be noisy and is impacted by the way it’s collected. Mining and exploration projects gather their data using drones, planes, and helicopter-based instruments.
AGS software accounts for each instrument’s unique information: the geometry, wave form, time gates, and the current and other specifications for how the instrument works.
“Having these correct specifications is extremely important to get the most reliable resistivity models from the survey data,” says Toke.
“There are a lot of filters you can apply to remove or smooth out noisy data.”
Using AGS QA/QC tools and instrument-specific processing, mining teams get better, cleaner data and can thus make more accurate and useful models.
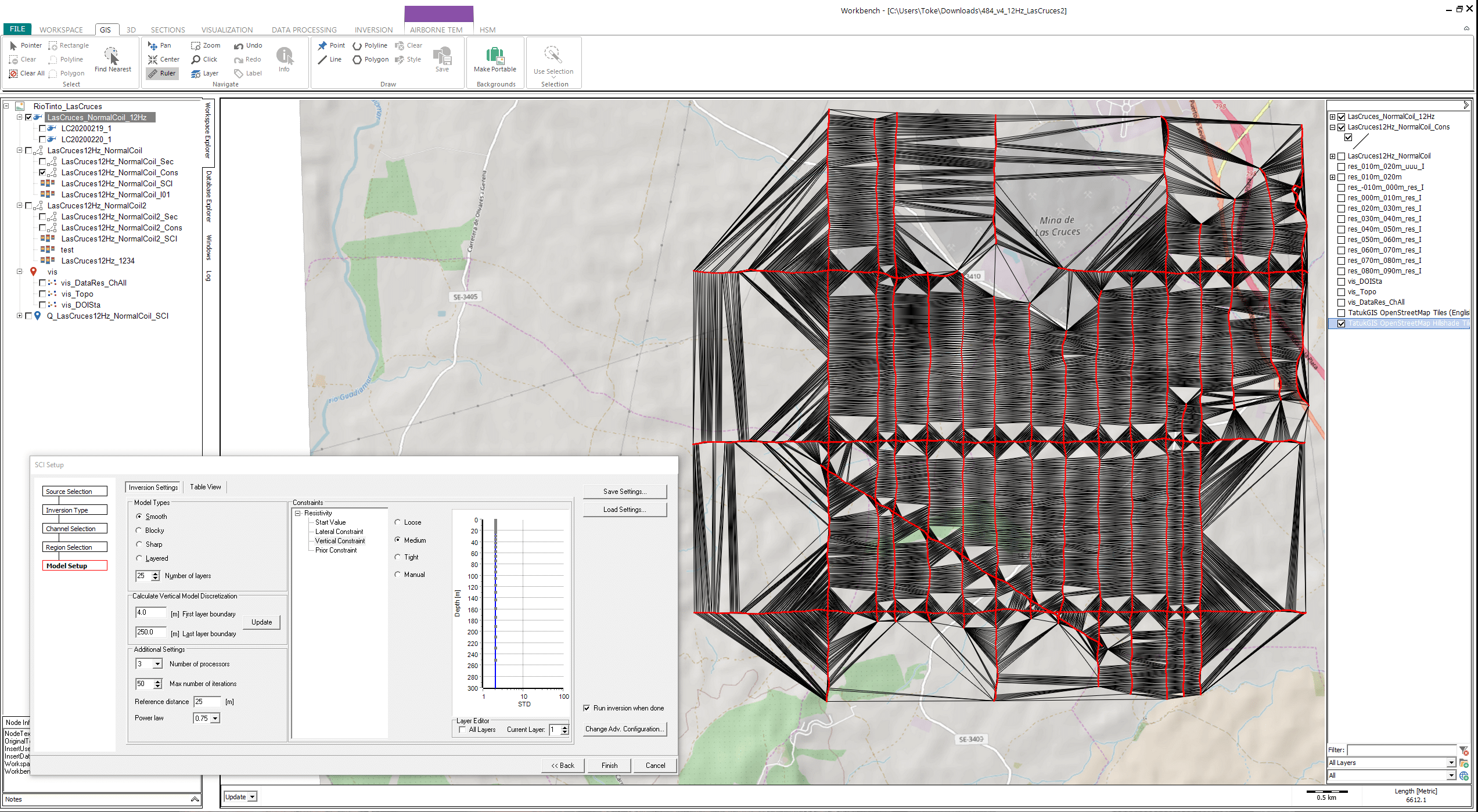
Display of the 3D constraints of the data in an inversion setup.
3. Cut out the IP effect
Another common issue with electromagnetic surveys is the induced polarisation (IP) effect. Even if the data collection is done perfectly, different structures in the surface and subsurface can create errors in the results.
Anyone who works with geophysics data is familiar (and likely frustrated) with the IP effect as it makes data useless – and models based on that data inaccurate.
“Often with TEM data in mining, the clay and minerals can create an induced polarization effect, an IP effect, in the data,” says Toke.
“In most cases, TEM data that has been affected by IP cannot be used. So, you need to remove this data before you create resistivity models. In Workbench, you can actually model for the IP effect in the data by using a Cole-Cole or MPA (Maximum Phase Angle) model.”
AGS inversion schemes can account for the IP effect and allow users to keep more of the data they have collected and use it for modelling.
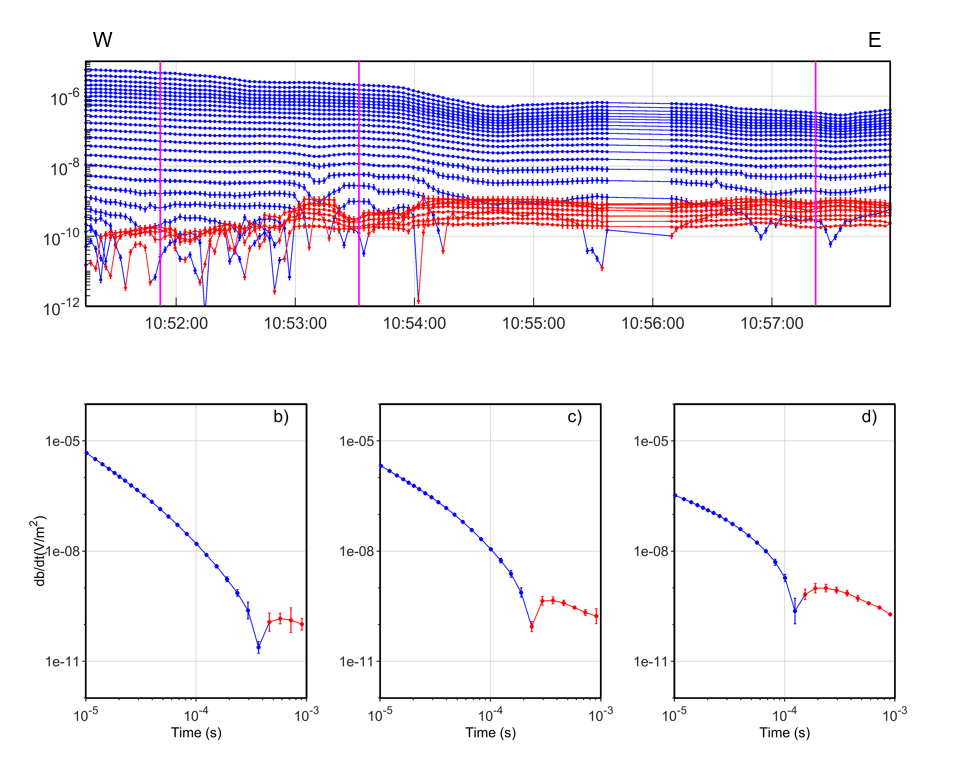
Looking for IP effects in the TEM data.
4. Using and protecting groundwater
AGS software was the result of a project to map and protect Denmark’s groundwater using geophysics. So far, they have mapped 40% of Denmark’s area and around 5,600 kilometers of buried valleys where the groundwater is located.
Over 20 years of expertise and insights within their software is now being applied by mines.
“Our software is used to find groundwater at mines for many reasons, primarily for extracting or processing minerals. However, if a mine goes below the groundwater table, it can deplete groundwater or create an inflow into the mine,” explains Toke.
“Groundwater is also a big risk for the mining operations. So, they often drain groundwater and AGS software can map the groundwater and help determine the direction of groundwater flow and quality of the groundwater, too.”
Flooding can be catastrophic to mine safety and operations. Also, the groundwater needed by local communities and ecosystems must be protected. However, mines need a lot of water nearby to process and extract the ore.
“Mines do aquifer mapping with AGS because they lack water to process the minerals and to extract the minerals,” says Toke.
Within AGS, teams can import borehole information and interpret it alongside airborne electromagnetics to find aquifers around mineral excavation sites. It also allows them to map groundwater extent, so they can avoid runoff and polluting other areas.
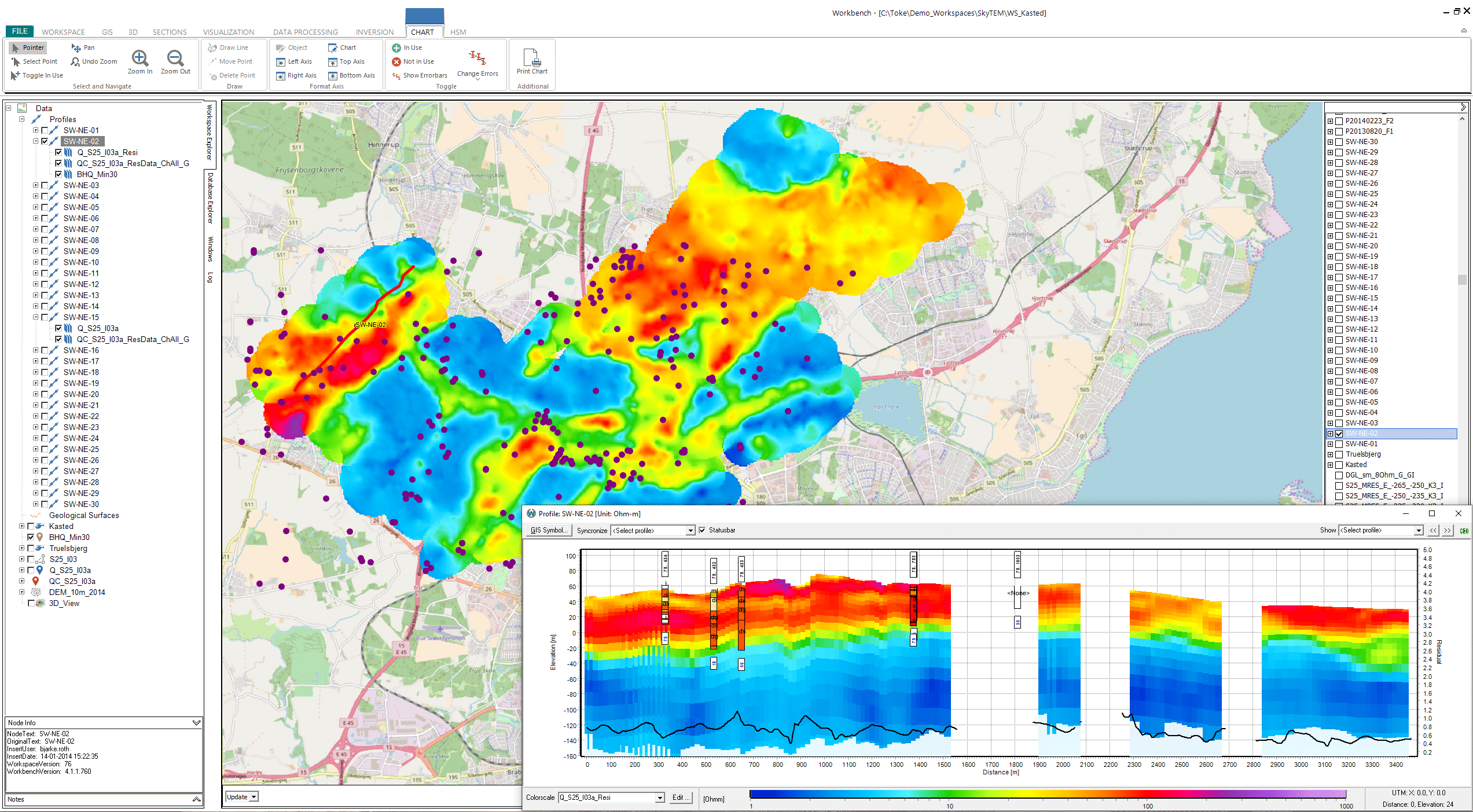
Looking for IP effects in the TEM data.
5. Planning and monitoring tailings
Tailing storage facilities are the most obvious place where groundwater is an important consideration. Placing them has major risks.
You need to understand the stability of the geology to ensure the area doesn’t deform or collapse, as well as knowing where groundwater is to avoid contaminating it.
“Another thing is the location of these tailing dams. It’s very important when they build tailings dams that they’re made so they don’t interact adversely with groundwater. Seepage should be minimised because it could contaminate the groundwater.”
Adhering to environmental regulations and minimising local impacts are key to mining operations. It ensures their social licence to operate – as well as avoiding the massive costs of cleanup.
“If tailings water seeps into the groundwater that will be a big problem. So, understanding the hydrogeology around mining areas is really important to avoid these major risks and environmental impacts.”
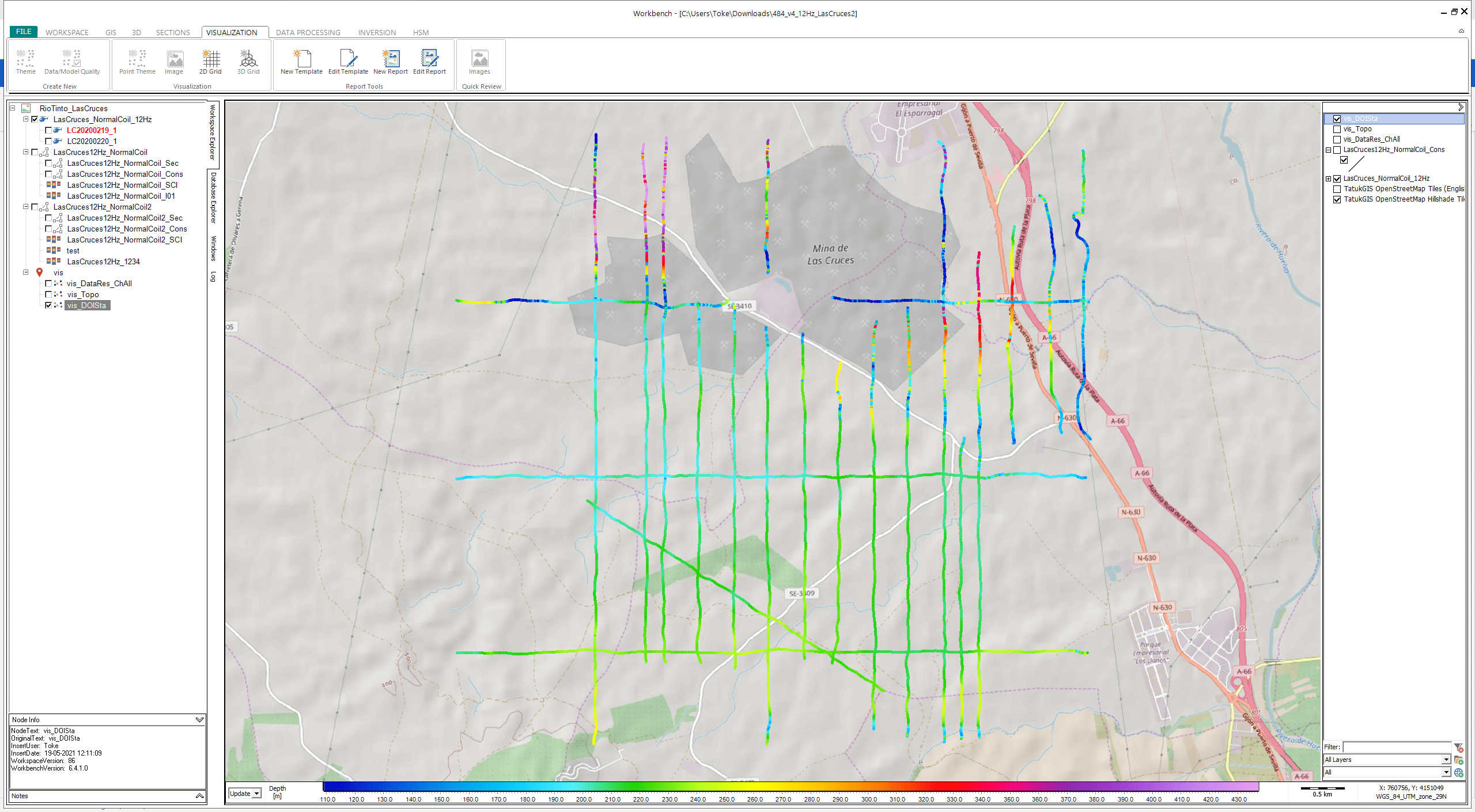
Displaying the Depth of Investigation (DOI) for each model. This will tell you how deep the models can be trusted.
What’s the future of resistivity models in mining?
As new types of sensors and surveys hit the market, they offer mining professionals the chance to get creative.
“They’ve even used AGS to find bedrock to determine where they can put the crusher machine,” says Toke.
AGS provides the link between geophysical survey instruments, resistivity modelling, and exporting those files into geological modeling tools, like Leapfrog.
Ensuring better data and bringing it all together creates a better understanding of the earth and groundwater, helping mining and exploration companies reduce risk.
Learn more about Seequent’s expanded portfolio of new solutions.