Swiss multi-national LafargeHolcim is at the forefront of sustainability and innovation and use Seequent’s solutions to help them along their journey. In 2015 they introduced Leapfrog Geo to improve their understanding of the complex Nobsa Quarry. As a result of this improved understanding the strip ratio has been reduced from 7:1 to 1.5:1, the resource base increased from two to 35 years and logistical operational savings of USD 2.5 million per year have so far been quantified.
The Project
LafargeHolcim is a world leader in the extraction and processing of Industrial Minerals and operate across 75 countries with 2,300 operating sites, ~72,000 employees and ~26.7 billion CHF net sales.
By the end of 2014, LafargeHolcim’s Columbia based Nobsa Cement plant, which sourced raw materials from three quarries including their own self-operated Nobsa Quarry, was at risk of stopping production due to a lack of raw materials. In 2015 a multi-disciplinary taskforce met to establish a sustainable solution that focused on maximising usage of the Nobsa Quarry. The cornerstone of the project was the reassessment and optimisation of the complex Nobsa deposit.
Leapfrog Geo was used to reassess and reinterpret the geology of the Nobsa deposit and to better manage the variability in material quality. Leapfrog Geo’s implicit modelling approach not only improved understanding and sped up the modelling process but allowed new information to be easily added.
Following this successful reassessment and clearer understanding of the resource, the block model was recalculated, and an integration extraction concept was established with QSO, LafargeHolcim’s system for scheduling and optimised dig management. This effective quality control of the materials constituting the raw mix has, for the first time, enabled strict implementation of the mine plan.
LafargeHolcim’s Group Lead Geologist, Rodolfo Vargas Pedroza explains, “The lack of a sound geological model made it difficult to properly model the material quality and develop a reliable mine plan as existing plans were frequently aborted when something unexpected was encountered. Using Leapfrog Geo we were able to better define and understand the Nobsa deposit. As a consequence, rather than sending the marginal material to waste, we can now define and blend the low grade with the limited high grade material we have modelled, increasing the resource base from two to 35 years. This has had a significant impact on strip ratio, reducing it from 7:1 to 1.5:1. We have also reduced the amount of limestone brought from external quarries, reducing operating cost by USD 2.5 million per year.”
Situation
The Nobsa Plant sourced raw material from three quarries, the nearby self-operated Nobsa Quarry and two other subcontracted quarries, located 7km and 30km from the plant. In 2014, the marginal quality of the Nobsa deposit, delays in permitting a new nearby deposit and increased costs due to an inability to accurately plan jeopardized extraction at Nobsa Quarry which was at serious risk of stopping production.
The Nobsa deposit is a complex geological body. The area consists of intense folding and faulting and the vertical nature of the interbedded limestone, marl and clay make exploration drilling arduous. The quarry lacked a high quality geological model which made it difficult to understand and therefore manage the variability in the quality of the material. Mine plans quickly became redundant due to unexpected variations in the geology.
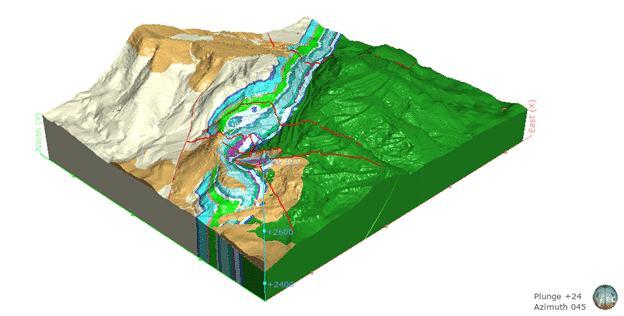
Figure 1. Geological model produced in Leapfrog Geo.
The inability to accurate plan also made it impossible to take full advantage of the deposit. Many layers of low-grade limestone were disposed of as a waste. To include them in the process, high-grade limestone imported from other quarries located more than 30 km from the plant was required.
Models were completed by traditional methods which was time consuming and unreliable. Due to a wide range of responsibilities, there was also a shortage of geologists with the time, skill and knowledge to build, estimate and report on the reserves. This also meant that models could not be updated with the latest information on a regular basis.
“Many layers of low grade limestone were being disposed of as waste. If we wanted to include them, we had to truck in additional high grade limestone from nearby quarries which wasn’t economically viable.”
Rodolfo Vargas PedrozaLead Geologist, LafargeHolcim Group
Response
Leapfrog Geo was introduced to quickly improve understanding of the Nobsa deposit. A key feature of Leapfrog Geo is that models are rapidly generated directly from data by the implicit modelling engine, bypassing time-consuming wireframing. Models are quickly visualised in 3D allowing teams to rapidly gain visual insights to guide interpretations.
Rodolfo explains, “We were impressed with Leapfrog’s ease of use, its speed and accuracy and its ability to rapidly visualise data. Due to the complexity of the deposit the ability to correctly domain different zones of geology, weathering and quality is critical, and we were able to achieve this with Geo. We were also able to apply variable trends to the data based on the structural interpretation of the different strata.”
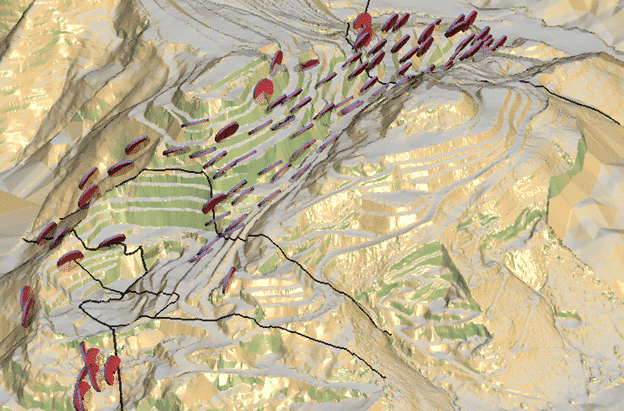
Figure 2. Structural trends defined in Leapfrog.
Using Leapfrog Geo the team were quickly able to improve their interpretation. Rodolfo comments, “We were able to better define black shale layers and spatial distribution of low grade limestone. We were also able to better define different rocks available in the deposit and determine how to extract most of the limited high grade layers to avoid waste of low grade limestone.”
Leapfrog Geo’s dynamic modelling feature also allowed new information to be quickly and easily added without the need to start the modelling process again. As new data is added to the model, the rules and parameters already set are automatically applied and models are refreshed with the new data. This dynamic updating feature ensures models are always up to date and available for mine plans to be adapted and optimised proactively.
Rodolfo says, “Being able to update easily is essential as we receive a lot of information as we extract materials and we need to be able to use that information to improve the models and our understanding. Without this we can’t make the best and most economic decisions.”
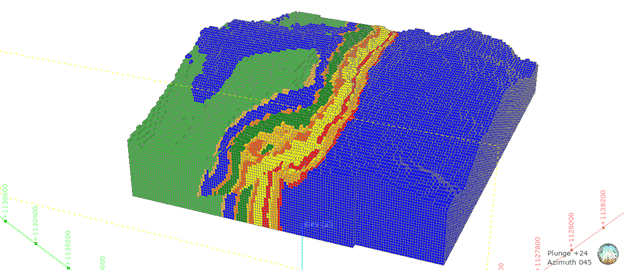
Figure 3. Using leapfrog to dynamically update block models with material quality.
Outcome
Following the reinterpretation of the geological model, the block model was recalculated and an extraction concept was established that looked to include all available materials in the raw mix, maximising the use of low grade material that was previously wasted and ensuring the strict implementation of the mine plan thorough quality control of the materials.
“After developing a proper geological modelling using Leapfrog Geo it was possible to determine the location and quantity of high grade limestone within the same deposit and establish a blending plan to use the low grade limestone in the process, avoiding our having to throw it away as waste. Identifying the pockets of high grade also means that we can minimize the incorporation of materials from distant quarries.”
Rodolfo Vargas PedrozaLead Geologist, LafargeHolcim Group
Maximizing the use of low grade material brought significant benefits:
- The raw mix resources increased from two to 35 years.
- Just looking at 2015, USD 665,000 were saved using low grade limestone that was previously wasted:
- 150,000 tonnes were included in the raw mix.
- 63,000 tonnes were used as a Mineral Component for Cement production (MIC).
- Stripping ratio decreased from 7:1 to 1.5:1.
- Reducing the transportation of high grade limestone from other quarries permitted saving an extra USD 2.5 million of operating costs.
- Significant environmental benefits with the reduction in the volume of material being dumped.
The environmental benefits gained from better understanding and sustainable management of the deposit will also help LafargeHolcim in pursuit of their 2030 Plan and Sustainability Commitment to create more value from waste by transforming resources for all production processes. This sustainable approach is also outlined in Imagine the Future with Industrial Minerals, Roadmap to 2050 by the Industrial Minerals Association-Europe (IMA-Europe). This Roadmap identifies several factors that contribute to zero-waste that LafargeHolcim now experience. These include extracting locally and reducing the need for transportation, the evolution of a true ‘materials science’ which through technologies such as Leapfrog transforms working practices, and contributing to a resource efficient economy, by using resources better at every stage of the supply chain.
“With an increasing focus on the environmental and social challenges related to mining, access to new resources is becoming more restricted, this requires companies to maximise the value they can extract from existing resources. Solutions like Leapfrog enable us to extract maximum value and be more sustainable.”
Rodolfo Vargas PedrozaLead Geologist, LafargeHolcim Group
LafargeHolcim has also introduced Leapfrog Edge, Leapfrog Geo’s resource estimation extension, which enables the streamlining of modelling and resource estimation into one smooth workflow. Edge allows for the integration of resource estimation with 3D geological models and as with Geo, any refinements made and new data added flows through and updates the resource estimate. Edge is highly visual and includes all the standard industry tools.
Seequent’s Account Executive, Europe, James Edwards comments, “Leapfrog Edge enables LafargeHolcim to accurately model the distribution of contaminant material, reducing uncertainty and providing a greater understanding of the natural variability of the resource. With the additional tools Edge provides, LafargeHolcim is able to take this data and define the material quality across the Nobsa deposit leading to more robust mine plans and ultimately ensuring maximum value is being extracted from the resource.”
The use of Geo and Edge is also adding to the capability of the team as the software is relatively easy to learn and quickly upskills. In the past there had been a lack of skilled modellers as it took time to become proficient in other software packages.
“We had lacked expertise with the knowledge, skills and competences to model, estimate and report reserves, we’ve been able to rectify this with the introduction of Leapfrog Geo and Edge.”
Rodolfo Vargas PedrozaLead Geologist, LafargeHolcim Group
Leapfrog is now being implemented throughout Lafarge Holcim to systematically update models, resources and reserves across their global operations.
Seequent’s Regional Director, EMEA, Luke Stewart comments, “We’re really pleased that our solutions are adding value through greater resource knowledge. This greater understanding of the location, quantity and quality of limestone in the Nobsa Quarry has helped LafargeHolcim in their pursuit of more sustainable mining, effectively leading to an increase in their resource base and reduction in operating costs. This is scalable for all types of operations, whether you have a small or large deposit we are consistently seeing the benefits/positive change being realised in the Industrial minerals Industry.”
If you’d like to read more about Seequent’s involvement in the Industrial Minerals sector, you can do so here:
Industrial Minerals: How to predict material quality faster and more accurately
Building better sustainability for Industrial Minerals Mining