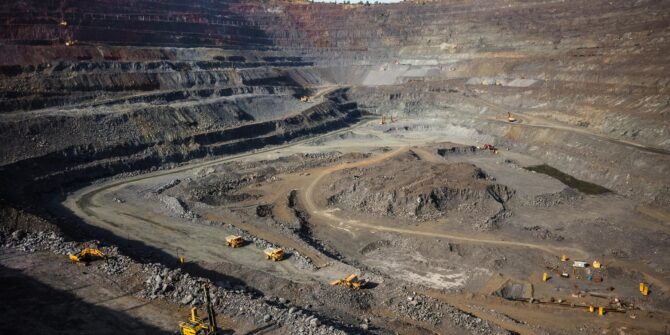
Webserie | Corto Plazo – Estimación de Recursos Aplicada al Corto Plazo | Episodio 3
Revisaremos la secuencia de pasos para la estimación aplicado a corto plazo empleando las soluciones de Seequent como Leapfrog Geo, Edge y Central donde se

Webserie | Corto Plazo – Modelado para Corto Plazo
Conocerás las herramientas y funcionalidades de Central y Leapfrog Geo con el objetivo de generar modelos 3D (Vein System); edición avanzada de vetas (hangwall y

Soluciones geotécnicas de Seequent para túneles – Parte 2 – Nuevas herramientas de análisis numérico
En este webinar, descubrirás cómo las soluciones geotécnicas de Seequent, con GeoStudio y PLAXIS, optimizan los análisis de estabilidad y deformación, integrando visualización 3D para

Geocast | Las Fronteras del Equilibrio Limite
Descubre cómo aplicar los límites del equilibrio límite en estudios reales de taludes. En este webinar técnico, abordaremos los métodos propuestos por John Krann y
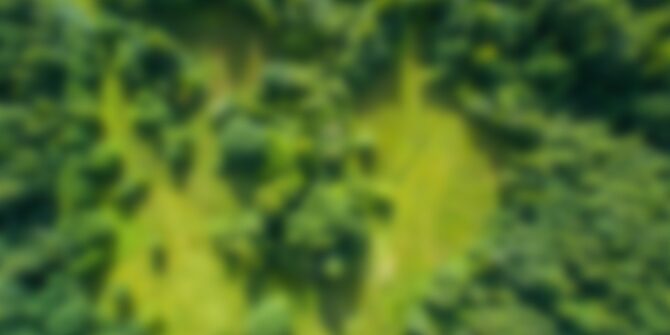
Vea las novedades de GeoStudio 2025.1
GeoStudio 2025.1 ofrece una combinación equilibrada de nuevas funcionalidades y mejoras para nuestras herramientas principales. Esta versión incorpora scripts de Python, lo que permite flujos

Oasis montaj 2025.1 Qué hay de nuevo
Join Laura Quigley as she walks through what’s new in Oasis montaj 2025.1, an update that reaffirms our commitment to advancing geophysics and improving data
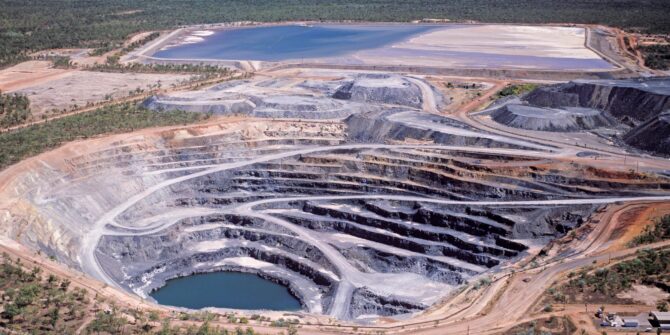
Webserie | Corto Plazo – Preparación de Base de Datos – Sesión 1
Exploraremos funcionalidades de Central y Leapfrog Geo para acceder y gestionar datos actualizados, analizar información de sondajes y puntos, generar compuestos, ingresar datos de mapeo/voladura
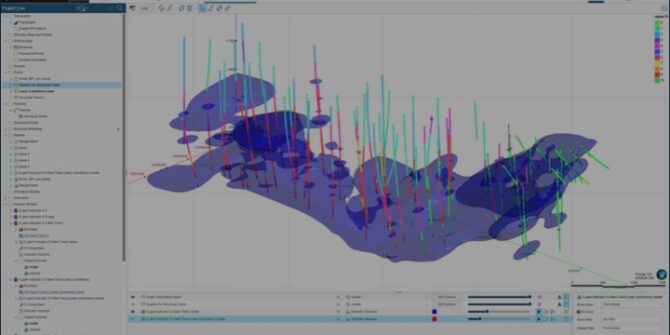
Optimización del modelado estructural en Leapfrog 2025.1
Acompañe a Andrew McLoughlin, gerente de Producto, en un análisis detallado de Leapfrog 2025.1, que presenta mejoras significativas en las tendencias estructurales.